Metalworking processes
We use various metalworking processes for materials that are difficult to machine. MTU Aero Solutions offers you access to these processes:
- NC/CNC-controlled milling
- NC/CNC-controlled turning
- NC/CNC-controlled grinding
- NC-controlled drilling
- NC/CNC-controlled electrical discharge machining
- ECM/PECM (precision) electrochemical machining
With the CNC technology can also be machined very complicated 3D contours.
Benefit from the advanced technology of our CNC manufacturing systems:
A further development of the classic ECM process is PECM (Precise Electrochemical Machining):
Major advantages of process at a glance:
Downloads
Contact
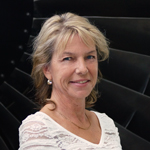
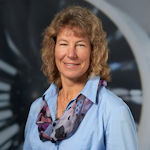