Joining – Welding – Brazing processes
We use various processes of joining, welding and brazing to get materials together. MTU Aero Solutions offers you access to these processes:
- Diffusion bonding
- Pressure welding
- Friction welding
- Manual and CNC-controlled TIG welding
- CNC-controlled laser welding
- CNC-controlled plasma welding
- EB welding
- Laser powder cladding
- Induction brazing
- High-temperature vacuum brazing
For example: Enertia friction welding
One of the key technologies for the manufacture of compressor rotors is friction welding. This joining technique is particularly suitable for rotors made from materials capable of withstanding higher stresses and for the larger rotors needed for the next generation of engines. Friction welding permits rotor components in titanium and nickel materials to be joined and produces weld joints of superior integrity. The compact rotors manufactured by friction welding weigh less and help cut fuel consumption.
Advantages:
- Short welding time and, as a result, low heat input and low distortion.
- High reproducibility of the weld quality.
- Static and dynamic strength of the joint within the scatter range of the basematerial characteristics.
- Non-melting materials can be joined by friction welding.
- Dissimilar materials, e.g. steels and nickelbase alloys, can be joined by friction welding.
- The joints are free from typical welding defects, such as pores, slag inclusions, shrinkage or solidification cracking.
- Owing to the high reproducibility, the length reduction can be kept within a tolerance of +/- 0.25 mm.
Downloads
Contact
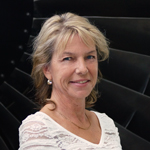
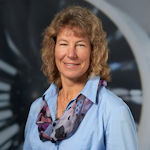