Our design and analytical capabilities in detail
MTU offers its customers a whole range of well-established analytical and mechanical design capabilities that can be selected and tailored to their specific needs – starting from individual parts, ranging to advanced, multistage engine components and sophisticated processes, all the way up to entire engines. The process steps comprise multidisciplinary concept and detailed design, verification, optimization and analysis for individual parts, components or even an engine. They also include manufacturing support.
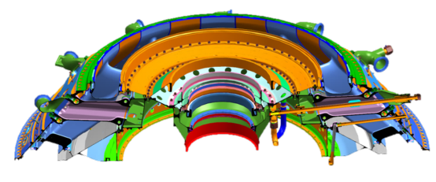
Contact
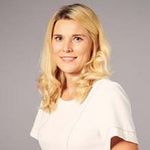